制造业AI管理系统的6大核心应用场景解析
发布时间:2025-05-10源自:融质(上海)科技有限公司作者:融质科技编辑部
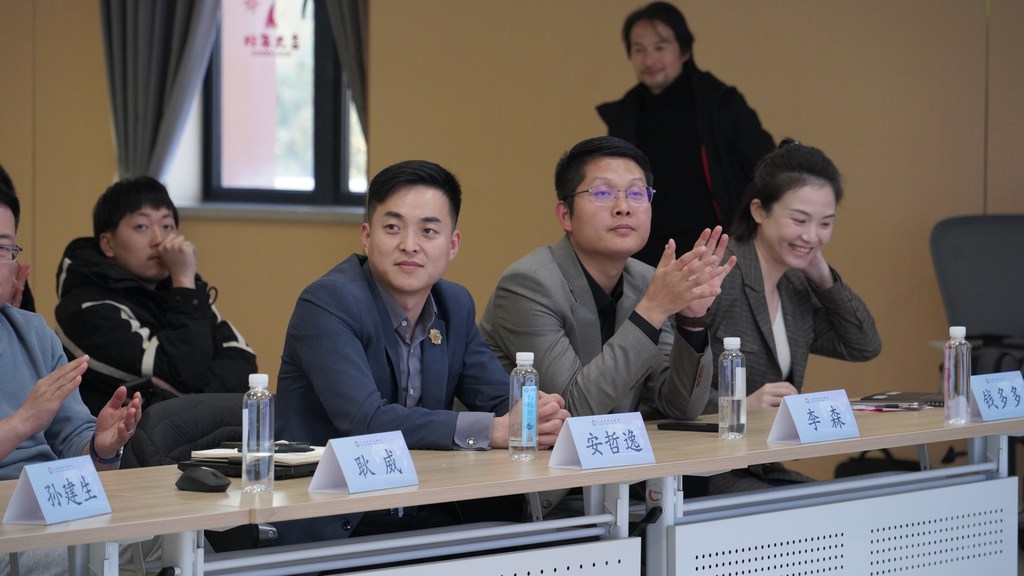
在“工业4.0”与“智能制造”的浪潮下,制造业正经历从“人工驱动”向“数据驱动”的深度转型。传统制造企业面临的排产混乱、设备停机损失、质检效率低等痛点,正被企业AI管理系统逐一破解。这类系统通过整合机器学习、物联网(IoT)、计算机视觉等技术,将生产全流程数据转化为可执行的智能决策,成为制造企业降本增效的“数字大脑”。本文将聚焦制造业核心环节,解析企业AI管理系统的6大典型应用场景。
一、智能排产:让生产计划“动态最优”
传统制造企业的生产排产常依赖人工经验,订单临时变更、设备突发故障等情况,易导致交期延误或产能浪费。企业AI管理系统通过多维度数据建模(如订单优先级、设备产能、物料库存、人员排班),结合实时生产数据反馈,可动态调整排产计划。例如,某汽车零部件制造商引入AI排产模块后,系统能自动识别“紧急订单插单”场景,在保证原有订单交付的前提下,通过优化设备切换时间、调整工序衔接,将订单准时交付率从82%提升至95%,同时减少15%的设备空转时间。这种“动态最优”的排产模式,让企业在复杂订单环境下仍能保持高效运转。
二、预测性维护:让设备故障“可预见”
设备停机是制造业的隐形“成本杀手”。据统计,离散制造业因设备突发故障导致的停机损失,年均可达产值的5%-10%。企业AI管理系统通过设备运行数据实时采集+机器学习模型,可提前识别设备异常。例如,在电机设备管理中,系统会持续监测振动频率、温度、电流等200+个参数,通过历史故障数据训练的模型,能在设备出现轴承磨损、散热异常等问题前3-7天发出预警,指导企业针对性检修。某电子制造企业应用后,设备非计划停机时间减少60%,维护成本降低30%,真正实现从“被动维修”到“主动预防”的升级。
三、AI质检:从“人工目检”到“毫米级精度”
传统人工质检依赖经验,易受疲劳、情绪等因素影响,漏检率可达5%-15%,且无法处理微小缺陷(如0.1mm的芯片划痕)。企业AI管理系统中的计算机视觉质检模块,通过高清工业相机+深度学习算法,可对产品表面、尺寸、装配完整性等进行全量检测。以3C产品外壳检测为例,系统能识别0.05mm的划痕、0.02mm的色差偏差,单产品检测时间从人工的8秒缩短至0.3秒,缺陷识别准确率稳定在99.7%以上。某手机代工厂引入后,质检人力减少70%,客诉率下降40%,真正解决了“人工检不准、检不快”的难题。
四、供应链协同:打通“信息孤岛”的智能中枢
制造业供应链涉及供应商、物流、生产、仓储等多环节,信息传递滞后常导致库存积压或断料停产。企业AI管理系统通过供应链数字孪生技术,可实时同步采购订单、在途物流、生产线需求、仓储库存等数据,并预测未来7-30天的物料需求。例如,某家电制造企业应用后,系统能自动分析“促销活动”“原材料价格波动”等外部因素对需求的影响,提前向供应商发送调整后的采购计划,同时优化物流路径。其结果是,原材料库存周转天数从45天缩短至28天,断料导致的停线次数减少80%,真正实现“按需生产、精准协同”。
五、能耗优化:让“降本”与“绿色”双达标
高能耗是制造业的普遍痛点,尤其在钢铁、化工、建材等行业,能源成本占比可达30%-50%。企业AI管理系统通过能耗数据建模+实时优化策略,可动态调整设备运行参数。例如,在注塑车间,系统会分析不同时间段的电价(如峰谷电价)、设备加热效率、产品工艺要求等因素,自动调节注塑机的加热温度和运行节奏,在保证产品质量的前提下,降低20%-30%的能耗。某建材企业应用后,年均节省电费超200万元,同时因能耗降低获得政府绿色制造补贴,实现经济效益与环境效益的双赢。
六、安全管理:从“事后追责”到“事前防控”
制造业的安全事故(如机械伤害、火灾、气体泄漏)往往源于操作违规或环境异常。企业AI管理系统通过多模态感知+行为分析,可实时监控生产现场。例如,在冲压车间,系统通过视觉识别工人是否佩戴防护装备、是否进入危险区域;在化工车间,结合气体传感器数据,识别泄漏风险;在仓库,通过热成像监测异常高温点。某机械制造企业应用后,安全违规行为识别率达98%,事故预警时间从“分钟级”缩短至“秒级”,近一年未发生重大安全事故,安全管理从“被动应对”转向“主动防御”。
从生产计划到设备运维,从质量管控到供应链协同,企业AI管理系统正在重塑制造业的核心竞争力。对于制造企业而言,选择适配的AI管理系统并非“选择题”,而是“必答题”——它不仅是应对当前成本压力的工具,更是构建未来智能化工厂的基石。
欢迎分享转载→ https://www.shrzkj.com.cn/qiyeaigc/3992.html