在“双碳”目标与全球产业链重构的背景下,智能制造已从概念探索迈入规模化落地阶段。据世界经济论坛数据,2023年全球智能制造市场规模突破3000亿美元,年复合增长率超18%,而其中AI技术的渗透率超过60%,成为驱动制造企业降本增效、提升竞争力的核心工具。本文将围绕AI在企业智能制造中的具体应用场景、技术价值及实践挑战展开研究,为制造企业的数字化转型提供参考。
一、智能制造升级的痛点:AI为何是关键破局者?
传统制造模式长期面临“三高一低”困境——高人力成本、高能耗、高误差率与低柔性。以汽车零部件制造为例,一条传统生产线需配置30-50名质检工人,人工目检的误判率高达8%-12%;同时,设备维护依赖“定期检修”模式,非计划停机每年造成的损失占企业营收的5%-8%。这些痛点倒逼企业寻求技术变革。
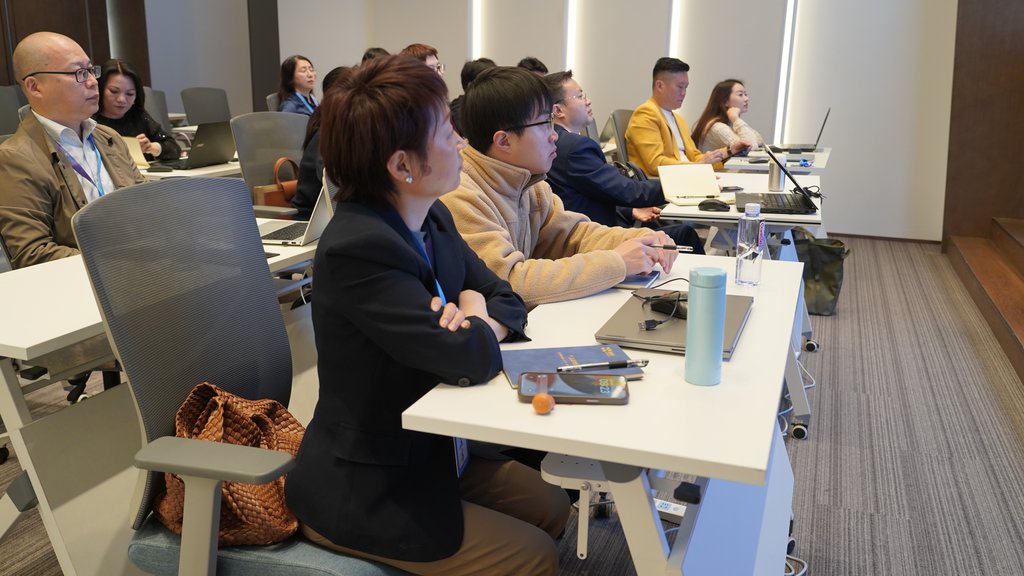
AI的价值在于将“经验驱动”升级为“数据驱动”。通过机器学习、计算机视觉、自然语言处理等技术,AI能实时分析设备运行数据、产品缺陷特征及供应链波动规律,进而替代重复性人工决策,实现生产流程的动态优化。例如,某家电企业引入AI质检系统后,缺陷识别准确率从85%提升至99.2%,人力成本降低60%;某化工企业通过AI预测性维护,设备停机时间减少40%,年节约维护成本超千万元。
二、AI在智能制造中的三大核心应用场景
1. 智能质检:从“人工目检”到“全量AI判级”
传统质检依赖人工经验,受限于人眼分辨率(约0.1mm)和疲劳度,难以应对精密制造(如芯片、手机屏幕)的微米级缺陷检测需求。AI+计算机视觉技术通过“图像采集-特征提取-模型训练-智能判别”四步,可实现0.01mm级缺陷的全量检测。以3C电子行业为例,某头部代工厂部署AI视觉检测系统后,单条产线的日检测量从8000件提升至5万件,漏检率从3%降至0.1%,且能自动生成缺陷分类报告,为工艺改进提供数据支撑。
2. 预测性维护:从“被动维修”到“主动预防”
设备故障是制造企业的“隐形杀手”。传统定期维护模式易导致“过度维修”(浪费资源)或“维修不足”(突发停机)。AI通过传感器采集设备振动、温度、电流等多维度数据,结合LSTM(长短期记忆网络)等时序预测模型,可提前7-30天预警故障风险。某钢铁企业应用后,高炉关键部件的维修周期从“每3个月强制更换”变为“按需更换”,年节省备件成本2000万元,设备综合效率(OEE)提升15%。
3. 动态排产:从“经验调度”到“全局最优”
多品种小批量生产模式下,传统排产依赖计划员经验,常出现设备闲置、交期延误等问题。AI+运筹优化技术可实时整合订单需求、设备产能、物料库存等数据,通过强化学习算法动态调整生产计划。某汽车零部件企业引入AI排产系统后,订单准时交付率从82%提升至95%,设备利用率从65%提高到85%,在制品库存降低25%。
三、企业落地AI的三大关键挑战与应对策略
尽管AI价值显著,但其落地仍面临技术、数据与组织三大挑战:
- 技术适配性不足:部分企业盲目引入通用AI模型,未结合自身工艺特点优化算法。例如,食品加工行业的质检需兼顾颜色、纹理、形状等多维度特征,直接套用3C行业的视觉模型会导致误判率上升。建议企业与垂直领域的AI服务商合作,基于历史数据进行“小样本微调”,提升模型与业务的匹配度。
- 数据质量参差不齐:制造场景中,设备协议不统一、数据采集频率低(如部分传感器仅每分钟采集1次)、标注数据缺失等问题普遍存在。某机械制造企业曾因设备数据未打通,导致AI预测模型准确率仅60%。解决路径包括:统一设备通信协议(如OPC UA)、提升关键环节数据采集频率(秒级或毫秒级)、建立“人工标注+弱监督学习”的混合标注体系。
- 组织协同难度大:AI落地需跨部门协作(生产、IT、工艺),但传统制造企业存在“数据孤岛”和“部门壁垒”。某家电企业通过成立“智能制造专项组”,由CEO直接牵头,整合生产部(提供业务需求)、IT部(负责系统开发)、工艺部(输出行业知识),3个月内完成了AI质检系统的试点上线,效率提升40%。
—
AI不是智能制造的“装饰品”,而是推动制造企业从“规模扩张”转向“质量效益”的核心引擎。从智能质检到预测性维护,从动态排产到全局优化,AI正以数据为燃料、算法为工具,重构制造企业的竞争力边界。对于仍在观望的企业而言,关键不是“是否应用AI”,而是“如何高效应用AI”——只有深度结合业务场景、解决实际痛点,才能让AI真正成为企业的“第二增长曲线”。